3 Key Benefits of Plasma Cutting
- By Admin
- •
- 24 May, 2018
- •
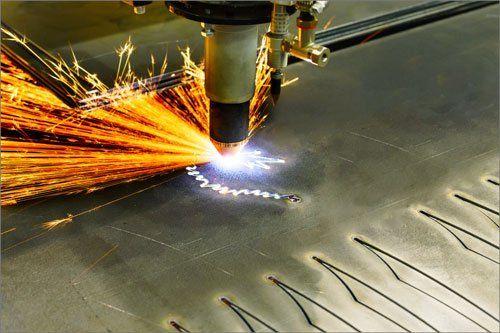
Metal fabricators use a variety of techniques to ensure clean, efficient cuts, including oxyfuel, laser, and water jet cutters. A newer yet increasingly popular technology goes by the name of plasma cutting. Yet many people - both amateurs and those within the metalworking industry - fail to recognize the distinct advantages offered by plasma cutting.
Unfortunately, this lack of awareness often leads to less efficient metal fabrication. Increase your knowledge of today's techniques for cutting and shaping metal. This article will help get you up to speed regarding plasma cutting, by discussing three of this technique's most notable benefits.
Unfortunately, this lack of awareness often leads to less efficient metal fabrication. Increase your knowledge of today's techniques for cutting and shaping metal. This article will help get you up to speed regarding plasma cutting, by discussing three of this technique's most notable benefits.
1. High Speed
Plasma cutting machines harness the power of electricity to cut through even the thickest sheets of metal. In order to focus this energy, a plasma cutter emits a high-powered stream of gas - usually argon, nitrogen, or oxygen. This gas acts as a conduit for the electricity, allowing the cutter to quickly achieve temperatures as high as 40,000 degrees Fahrenheit.
These incredible temperatures allow plasma cutters to slice through metal with incredible speed. The beam of a plasma cutter can cut through a 1.25-inch thick sheet of metal in roughly 1.5 seconds. By comparison, it would take an oxyfuel cutter roughly 20 seconds to accomplish that same task.
The speed of a plasma cutter gives it an incredible edge in efficiency. Simply put, manufacturers can get more work done in a shorter period of time when using a plasma cutter. This allows manufacturers to keep costs as low as possible, passing savings along to their customers in the process.
These incredible temperatures allow plasma cutters to slice through metal with incredible speed. The beam of a plasma cutter can cut through a 1.25-inch thick sheet of metal in roughly 1.5 seconds. By comparison, it would take an oxyfuel cutter roughly 20 seconds to accomplish that same task.
The speed of a plasma cutter gives it an incredible edge in efficiency. Simply put, manufacturers can get more work done in a shorter period of time when using a plasma cutter. This allows manufacturers to keep costs as low as possible, passing savings along to their customers in the process.
2. Versatility
Traditional cutting methods like oxyfuel use the power of oxidation to melt through metal. While effective on certain metals - steel and other ferrous metals- non-ferrous metals resist the process of oxidation. Stainless steel and aluminum, to name a few, exhibit poor behavior when cut with an oxyfuel torch.
Not only will it take oxyfuel a long time to cut through such metals, but it often leaves them excessively warped at the end of the process. Likewise, a large amount of dross - an unwanted byproduct of cutting - will be left behind. For these reasons, most metal fabricators consider oxyfuel off limits when it comes to such metals.
Plasma cutting knows no such limitations, thanks to the fact that it utilizes the power of electricity to cut metal. Plasma cutting requires only that a material possesses basic electrical conductivity. Nearly all metals meet this simple criteria. As a result, a single plasma cutter can do the work that it would otherwise take an arsenal of different cutters to accomplish.
Not only will it take oxyfuel a long time to cut through such metals, but it often leaves them excessively warped at the end of the process. Likewise, a large amount of dross - an unwanted byproduct of cutting - will be left behind. For these reasons, most metal fabricators consider oxyfuel off limits when it comes to such metals.
Plasma cutting knows no such limitations, thanks to the fact that it utilizes the power of electricity to cut metal. Plasma cutting requires only that a material possesses basic electrical conductivity. Nearly all metals meet this simple criteria. As a result, a single plasma cutter can do the work that it would otherwise take an arsenal of different cutters to accomplish.
3. Future Friendly
Traditional fabrications methods have earned their place in the metal cutting world. Many of these methods have stopped growing and adapting. Plasma cutting, on the other hand, continues to undergo an exciting process of refinement and development.
Plasma cutting equipment manufacturers understand the importance of keeping pace with the rest of today's technology. For instance, many newer models of plasma cutters allow access to key information through smartphone apps. These apps allow users to monitor information regarding their plasma cutter's power settings.
Plasma cutting has also embraced current trends in robotics, CNC machining, and CAD/CAM design technology. Such features allow metal fabricators to remain in-step with the contemporary world, thus keeping relevance in a time of increasing change and development.
Plasma cutting offers a number of highly exciting prospects - both in the present and the future. For more information on how plasma cutting can meet your metal fabrication needs or to get started on your plasma cut fabrication project, please contact the pros at Knowlton Industrial Steel Supply.
Plasma cutting equipment manufacturers understand the importance of keeping pace with the rest of today's technology. For instance, many newer models of plasma cutters allow access to key information through smartphone apps. These apps allow users to monitor information regarding their plasma cutter's power settings.
Plasma cutting has also embraced current trends in robotics, CNC machining, and CAD/CAM design technology. Such features allow metal fabricators to remain in-step with the contemporary world, thus keeping relevance in a time of increasing change and development.
Plasma cutting offers a number of highly exciting prospects - both in the present and the future. For more information on how plasma cutting can meet your metal fabrication needs or to get started on your plasma cut fabrication project, please contact the pros at Knowlton Industrial Steel Supply.
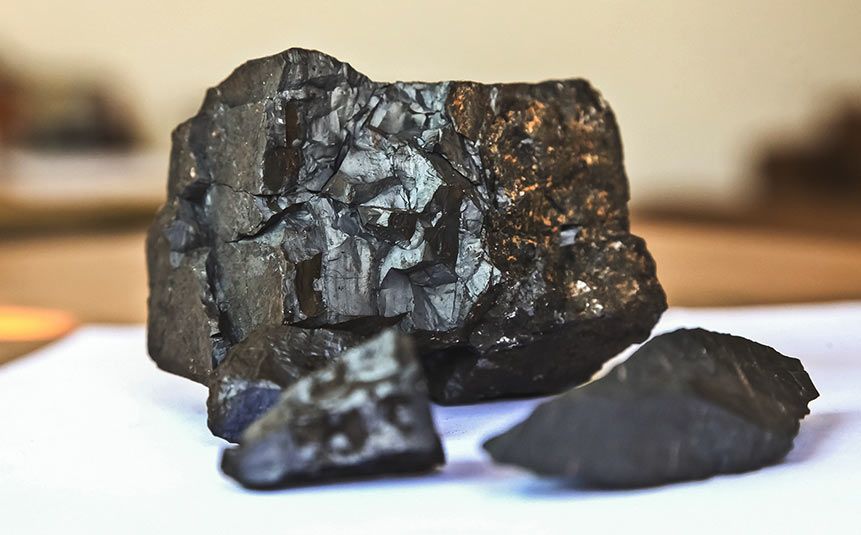
Steel holds an abundant place in the modern world. You can find steel anywhere from automobiles to high-rise buildings and industrial processing equipment. Many different types of steel exist, each of them being a slightly different alloy with iron as its base metal. Manufacturers then add other elements to boost the overall performance of the hardened steel.
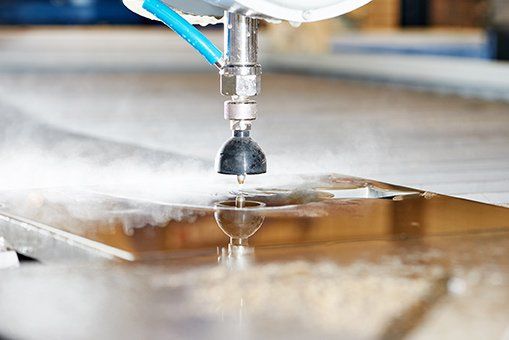
When you need to manufacture small or otherwise precise parts and tools, you face a wealth of options. Water jetting is a relatively new but increasingly popular choice among businesses, particularly if you work with dense or heat sensitive materials. Consider the following information about water jetting as you plan and design your components and the tools needed to work with them.
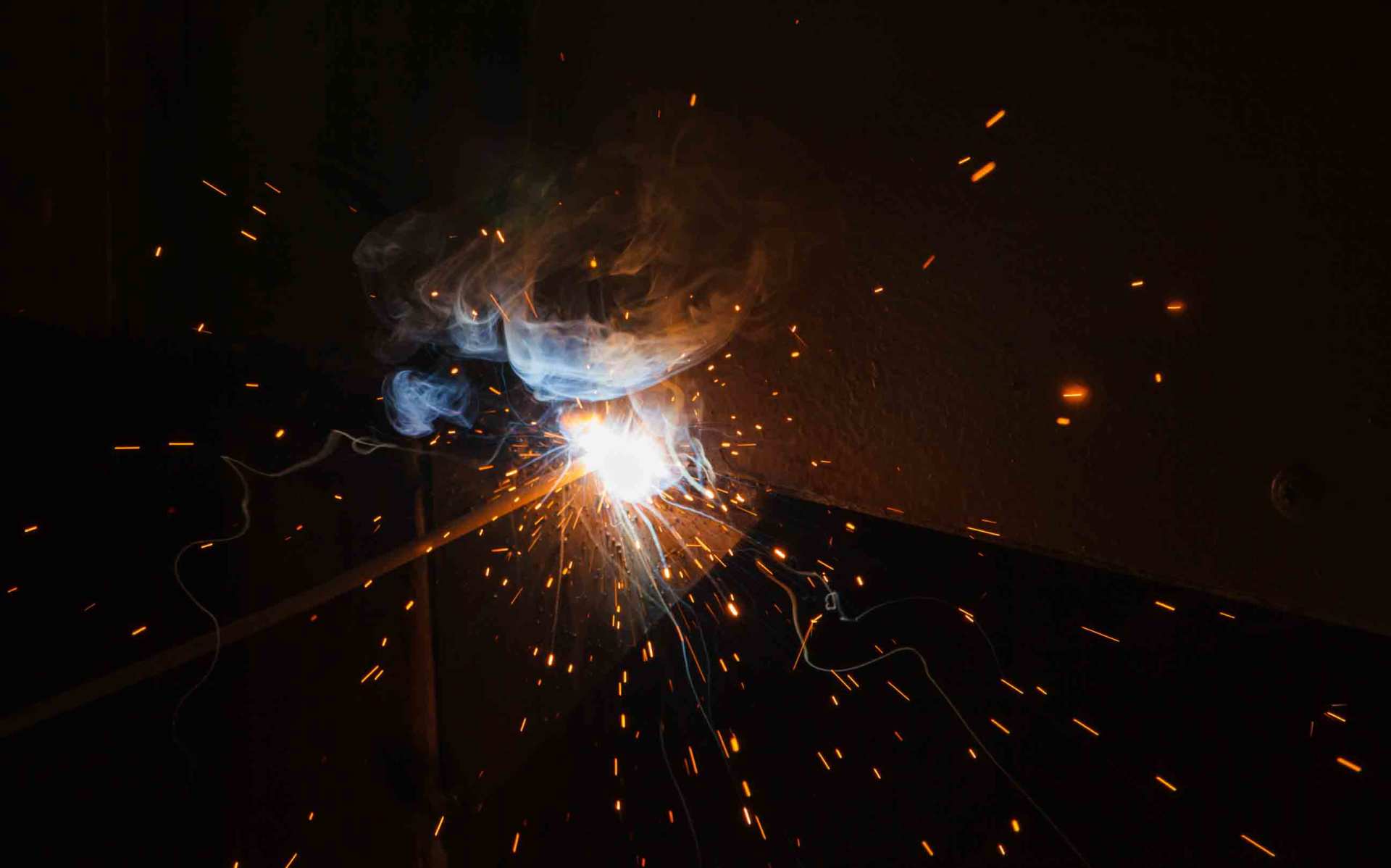
On the surface, the fundamental principle of welding is deceptively simple: high temperatures fuse together two or more pieces of metal. While this may be accurate in the most basic of terms, the actual art of welding remains much more complex. To get the strongest possible results, a welder must utilize the most appropriate welding method.
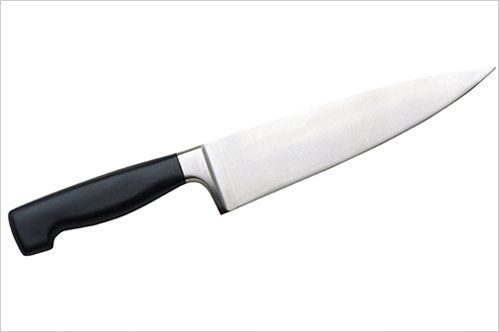
While knife and blade making is a skill many might associate with an era long gone by, it's one of the hottest growing DIY trends. Whether you want to simply use grinding tools to cut and polish a knife or feel ready to go all out with a forge and an anvil, you need the right kind of steel to get good results.