Using Water Jets to Cut Unique Parts and Tools
- By Admin
- •
- 27 Mar, 2018
- •
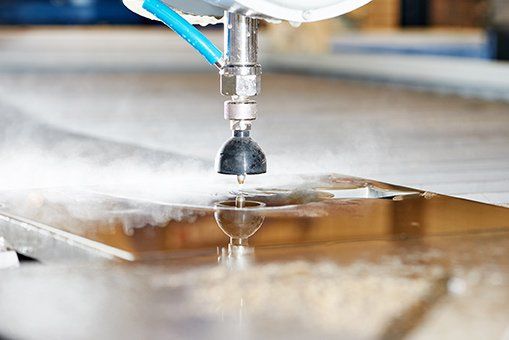
Understanding the Water Jet Process
If you have ever visited the Grand Canyon, you are probably already familiar with the immense potential strength of water. Given enough time, water naturally erodes just about any material blocking its way. Instead of grinding or splitting with lasers and plasma, water jets concentrate the erosive might of water into a tiny, high-pressure stream. Some machines use pure water to saw through materials, while others mix in abrasives for an added kick.
Either way, the result is a fast, powerful, and versatile fabricating process that can handle both heavy layers of steel and fragile aluminum sheets. The water never dulls or chips and is highly flexible, able to manufacture parts in a wide range of widths and shapes. If you work with objects that are thicker than a laser cutter can handle, but you need more accuracy than plasma, water jets are likely your most efficient choice.
Cutting With Precision
The high velocities and pressures typical in water jetting allow for both power and precision. When funneled down to a narrow stream, water jets reach minimum tolerances of about .002 inches, though this may vary by model and project. This is only slightly lower than the best laser cutters and much better than a typical plasma cutter.
Avoiding Heat Zones
In other cutting methods, the energy traveling between a material and the cutter generates a lot of heat. While some materials withstand high temperatures without issues, others respond chemically to the heat, changing their structure around the edge. This may not matter much for a large steel object, but precision tools can't afford to be warped and weakened.
Stainless steel, plastics, laminates, rubber, foam, and heat-sensitive alloys are just a few examples of materials that are best cut without these extra pressures. Even more tolerant metals, however, may benefit from a low-temperature cut. If you need a part to function exactly as intended, with no unpleasant surprises, water jetting is often the safest option.
Choosing Your Materials
This freedom from heat opens up endless possibilities when it comes to designing components. With water jets, you never need to compromise to produce a working part or tool. There are a few materials that cannot be cut with lasers due to their reflective surface. Copper, for example, is generally too bright for a laser cutter. However, no such problem exists with water jets, which can cut stone, wood, glass, and more.
Reducing the Need for Secondary Processing
A part may come out of fabrication looking pristine, but if you magnify its edges, any flaws in the cut will quickly become obvious. Chips, burrs, and rough corners are all hallmarks of laser cutting that must be minimized later on. Like the smooth sides of a canyon, water jets wear edges down to a smooth finish. In most cases, no extra processing is necessary.
Water jetting is one of the most powerful tools in our arsenal, but it is far from the only solution to a fabricating problem. If you still aren't sure which cutting process will deliver the right mix of quality, speed, and cost for your project, contact our experts today at Knowlton Industrial Steel Supply. Our professionals will go over your project requirements to ensure that you walk away with precisely the parts and tools you need.
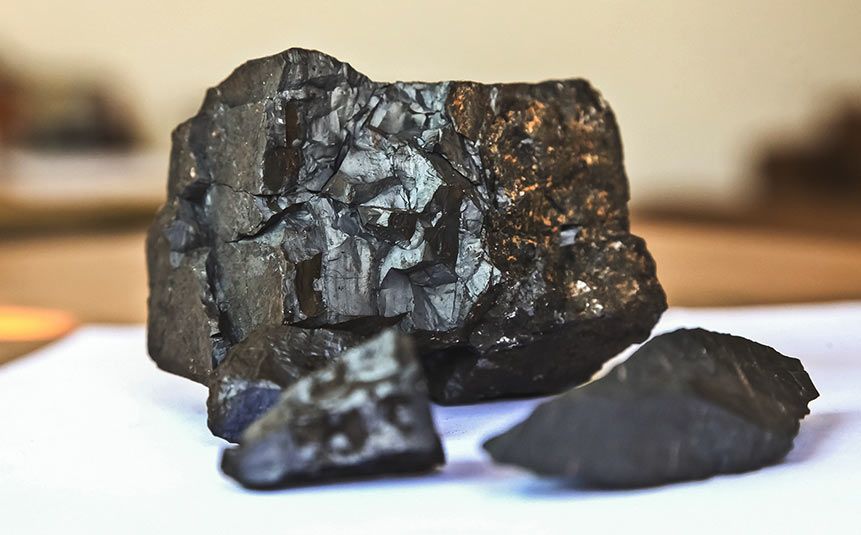
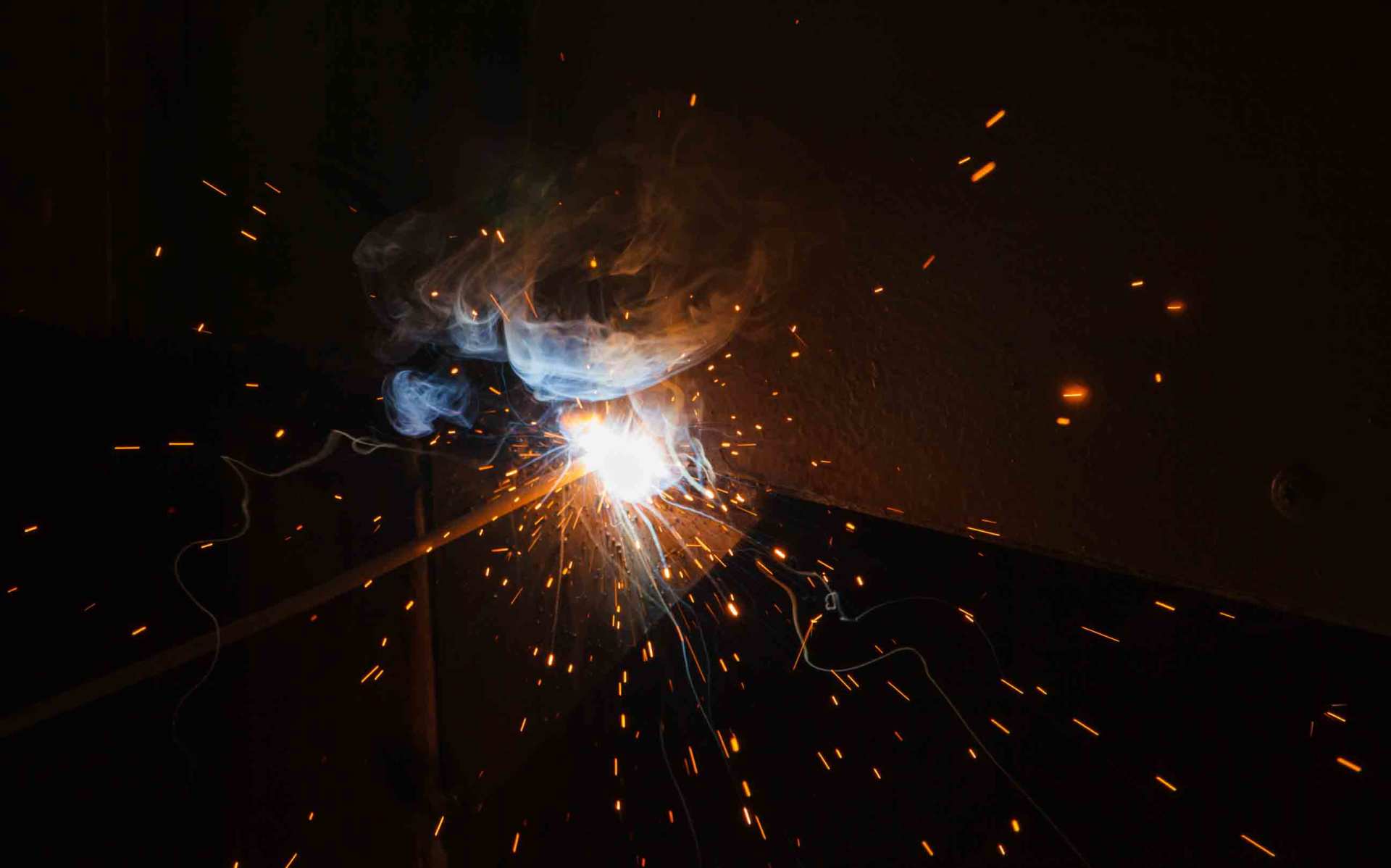
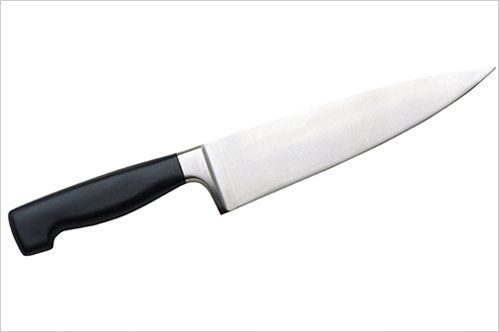